Chiller AC Maintenance
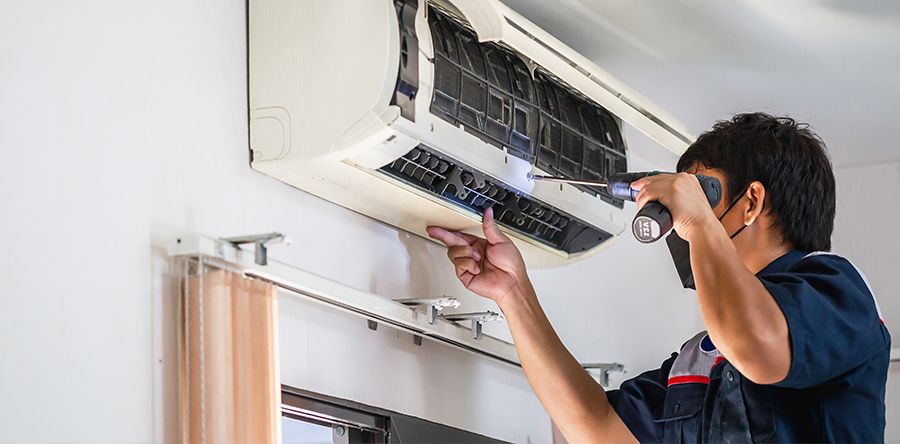
Any piece of machinery will endure typical damage that occurs over time. That is why it is vital to be comfortable with your company's industrial chiller. Maintenance of huge equipment pieces is critical to ensuring the equipment's lifetime and efficiency. A satisfied chiller results in a satisfied bill. Using our chiller maintenance checklist to reduce equipment faults and downtimes might be an efficient way to cut expenses in your business. Here are a few tips for keeping your industrial chiller in good working order while preventing catastrophic failures.
Chiller maintenance checklist
When it comes to maintenance, tracking daily activities is half the battle. Keeping a complete diary is the most effective way to understand your chiller’s performance. These logs should include flow rates, operational temps, voltages, and fluid levels. Virtual control systems are also often used to maintain daily records on machines. It takes less time and may be updated as frequently as needed because it is typically an automated system. Many times, remote monitoring solutions may also automate insight reports for real-time diagnosis on your chillers.
- All water intake vents and outputs must be inspected for leaks regularly.
- All parts of the compressor unit are essential to check, including tests for oil levels, leaks, vibrations, and fluctuations in operating temperatures.
- Power switches should be examined and cleaned.
- Filter dryers should be inspected, and unclean, outdated, or broken filters changed completely.
If you’re dealing with a new chiller, it’s the usual procedure to change the oil and filters after the first year.
Safety control of chiller AC
A chiller is consists of a compressor, an evaporator, and condensers. Each chiller requires a unique configuration matching the load for the best efficiency. Every chiller features safety controls to keep the cooling system safe, which safeguards against low refrigerant temperature, oil pressure, and excessive condensing pressure.
Utilization limits and refrigerant flow controls are two examples of these controls. The chilled water’s temperature is regulated by capacity controls, and refrigerant flow controls are modified once the compressor is in use. If these controls fail, the device has the option to shut down. It prevents more catastrophic machine damage, which might impact the health of persons around.
Focus on the tube and keep them clean
Tubes are the primary heat transfer channel in chillers and are significantly critical to the operation of your commercial chiller. Pollutants and particles can enhance thermal resistance, and it would limit heat transfer efficiency because the resistance would disrupt the consistency of approach temperatures in the chiller. It is critical to brush these tubes at least once a year. With an excellent monitoring system, you can detect issues before they develop. Allowing you to clear the tubes before they turn into a major issue.
Examine the water condenser
Lowering the water’s temperature when approaching the condenser of an industrial chiller enhances efficiency since it needs to work less to achieve its overall cooling effect. Although it is not suggested as a normal approach, lowering the temperature of the water going through the chiller’s condenser unit may temporarily solve difficulties with its coil.
Inspect the compressor oil
If you’re dealing with a new chiller, it’s the usual procedure to change the oil and filters after the first year. In addition, evaluate the oil to estimate the frequency of future oil changes. The dirtier your system, the more frequently it will require a replacement. We also recommend performing a spectrometric chemical study on this oil once a year, and it will help you become acquainted with your system and its possible faults. Learning how to deal with a variety of issues, ranging from excessive water content to the size of particles polluting the oil, is beneficial. Several chillers have removed oil from the mix, minimizing possible chiller maintenance expenses.
Detoxify the system
This method is only applicable to low-pressure machinery. It entails purging the network of semi-gases. These gases can be produced in a chiller’s low-pressure side using a pump or filter. Because the evaporators function in a vacuum, these non-condensable components can get in. Purge the air and moisture to ensure they are at an all-time low.
Examine the refrigerant leakage
The proportion of refrigerant flowing through a chiller’s compressor determines the rate of cooling. Valve stems might vibrate loose and cause refrigerant leakage. Refrigerant leakage from the compressor or the entrance of humidity into the system can also influence the chiller’s cooling capability. Checking for breaches and preserving a sufficient amount of refrigerant in the compressor unit of the chiller will guarantee top performance.
Maintain the flow
The flow of water, like the temperature, has a significant impact on the effectiveness of your boiler. The cold water rate must be more than 3 ft/s but much less than 12 ft/s. If your flow slows to less than 3 feet per second, it might develop laminae. When the flow rate exceeds 12 feet per second, vibration and noise provide an excellent condition for tube erosion.